Let's Talk Shop: New Design Lab
- Metal Museum
- Oct 23, 2019
- 4 min read
Updated: Jan 24, 2020
By Robert Fairchild, Arts Intern in Marketing
The Metal Museum has added a brand-new design lab to its facilities! Thanks to a matching grant from the Jeniam Foundation, the Museum now has a designated computer for design work, a 3D printer, and a 3D scanner. The computer has the capability to run 3D modeling programs, including Rhino and Fusion 360. It also runs support programs for the newly acquired 3D printer and 3D scanner. These additions will equip the Foundry and Smithy with the latest technologies as part of their design process.
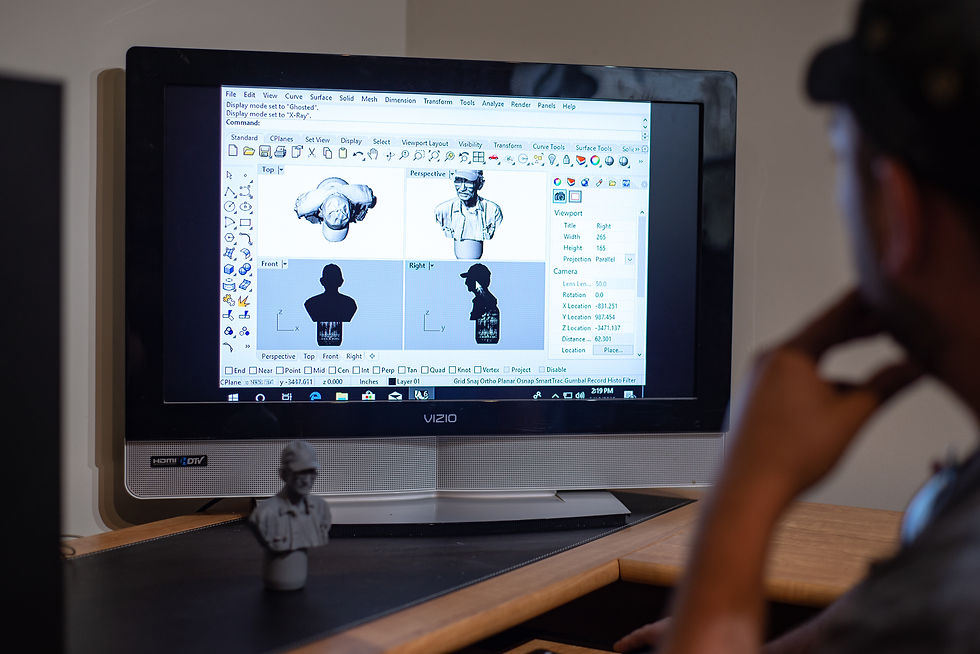
The design lab will be incorporated into several stages of planning and production. Whenever the shop has a proposal to complete, they can now create maquettes, scan them, and place them into real world scenes (such as the site where the sculpture will be). This means that when hearing concepts for public arts projects, clients will be able to visualize the final project onsite – before production has even begun. Another advantage to the design lab is the ability to create low-cost prototypes. 3D prints of new product designs will give the Smithy and Foundry an understanding of each product’s functionality and ease of use. Any flaws can be identified and corrected early in the design process.
Foundry Operations Manager, James Vanderpool, says that this new technology “will enable us to be even more independent with our pattern work.” Traditionally, patterns used in sand casting are made from wood. Today, the Foundry uses several techniques to cast patterns, including plaster modeling, oil-based clay, wax, and 3D printing. Patterns can be scanned into a computer system using the 3D scanner. If any are damaged, they can easily be reprinted. All pattern work can be done in-house with these latest additions to the design lab! They will be especially helpful with type-based projects that contain specific fonts and logos. 3D printing technology will allow for greater complexity in cast artwork as well. Small busts and other detailed models can be invested into ceramic shell, and then melted out of the ceramic shell to create molds for the Foundry. The Metal Museum staff is currently familiarizing themselves with these new processes and software programs. “Because most of the artists here at the Museum are very classically trained in metal work, we don’t have a lot of background in things like 3D modeling [or] 3D printing,” says James. Artists in the Museum’s apprenticeship program will also have the chance to test these new technologies during their residencies. The apprenticeship program supports the livelihoods of metalsmiths by honing their skills and preparing them for the next step in their careers. Because they are involved in all steps of the commission process, apprentices learn how to bid projects, apply for public arts projects, and work with clients throughout the creation of a piece. They can now add proficiency with CAD software, 3D printing, and 3D scanning technology to their many skills. This gives artists a competitive edge as they continue their careers beyond the Museum.

But shop staff and resident artists aren’t the only ones who will benefit from this new equipment! The education and curatorial departments will be using the design lab as well. Objects from the Permanent Collection can now be scanned, with the consent of the artist, and 3D printed for the public to touch and hold. Visitors with visual impairments will be able to have a tactile interaction with the work on display. In addition to allowing differently abled guests to experience the artwork, these 3D scanning and printing capabilities will be an invaluable teaching tool during classes, workshops, and other educational programs. The possibilities are endless.
The addition of the design lab means the Metal Museum is better able to serve its mission to preserve, promote, and advance the art and craft of fine metalwork. According to James Vanderpool, “[…] we can’t solely rely on traditional techniques we have been using.” By incorporating innovative technology into our studio practice, the Museum is moving the field forward, with a lasting impact on artists and visitors alike. We are all excited to see what this will help us achieve in the years to come.
Our lab is equipped with a Form 2 3D printer. As an SLA printer, it uses a resin bath and a UV laser to create printed objects. The finite laser hardens the resin, which gives prints incredible detail. Two other units come with the 3D printer – a cleaning and a curing system. When prints are completed, the build is placed into the automated washing tank that removes the “resin goop” from it with isopropyl alcohol. After cleaning it goes into an automated UV curing system. By using the same wavelength of light used in the printing process, it hardens and strengthens the print. Once this process is complete, you’re left with a very durable print that can be used as a pattern or a maquette.
Robert Fairchild is the Summer 2019 Arts Intern in Marketing at the Metal Museum. Fairchild is a senior at the University of Memphis, studying Studio Arts and Creative Mass Media. The Arts Intern program, which offers paid internships in the arts to undergraduate students in financial need, is one of many arts programs run by the Studio Institute.
Comments